Cheryl Miller posted on October 25, 2022 07:26
Seven Technologies from Two Cartoners to One Case Packer
… using Slug Accumulation, Micropitch & 90°Transfers, Curves & much more.
Multi-Conveyor (Winneconne, WI) - Multi-Conveyor recently built a series of independently powered conveyors to reorient various size cartons of product for inspection, fed from two cartoners, merging to a single case packer. Wide-side leading product end transfers from the cartoners, then rotate 90° in orientation, merges to a single lane, and then end transfers again to meet the designated case packing position.
The video shows an initial section where cartons are controlled using a tool-less adjustable pneumatic carton clamp assembly at the discharge, and an overhead pneumatic carton stop assembly end, where they will accumulate to a desired count. Customer supplied controls stop accumulated product allowing a pneumatic right angle pusher assembly to transfer product from one conveyor to the next. After the pusher retracts, the cartons release the next batch of accumulated product.
Tom Wright, Account Manager at Multi-Conveyor, explains: "The overhead carton stop comes down in front as the product backs up. This is the pneumatic clamp that comes up against the product. We let this group, or this slug, advance forward to this position which is going to transfer the group onto the main line and ultimately will continue to convey the products. We’re going to speed them up to create a larger gap so when we make the right-angle transfer there’s enough room between them.”
The shorter product size is conveyed through two friction top belts and a slave-driven micropitch transfer that create the necessary gap needed for the curve ahead. Tom continues, “With the shorter product length, we incorporate micropitch transfers for end-to-end transfers. And then what we have is another friction insert chain that’s going to grab that product at a faster speed to increase the gap between products to help assist at that 90° transfer.”
Belt coloring was specifically requested to contrast carton graphics which helps identify compromised product. Tom details the strategy, “A portion of this conveyor has a black or different darker color of carry surface for a customer supplied inspection camera that will look for deformities or irregularities of this carton that will stop the line allowing the operator to reject that product out.”
Other technology built into this system includes right-angle transfers; 90 degree side-flexing curves; simplistic bump turn; LBP (low back pressure) transitions; even slight elevation changes. All working in tandem to inspect, merge and ultimately position product to feed the customer’s existing single case packer.
Watch this brief video to see the system in action: https://youtu.be/GbaR1CReKTA Then, see even more conveyor merge or conveyor fed case packing videos by visiting our video gallery.
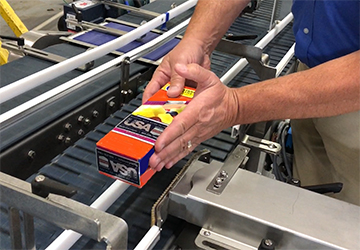
If you have any questions about this tecnology, please call: 1-800-236-7960