Weyco Group Crushes Cyber Week
...with the help of Multi-Conveyor inclines, declines, curves, diverts, rejects and more!
Winneconne, WI – Multi-Conveyor recently installed a masterful new conveyor system for a globally operated mail-order footwear giant, Weyco Group (NASDAQ: WEYS), headquartered in Glendale, WI. The goal? Crushing cyber week.
The 1.2 million square foot facility moves individual “pairs” of six major shoe brands over 13.5 miles of overall conveyance, from pick to ship. Multi-Conveyor was the first OEM supplier to install automated conveyor systems within their production floor that incline; overhead transport; decline; 180° curve; accumulate; justify; divert and reject.
George Sotiros, Chief Information Officer, Vice President of Distribution and Vice President of Information Systems explains the challenge: “Last year, prior to this cyber weekend, we would have to work overtime for a week and a half around cyber weekend. We’d have to work Saturday 10 hours, Sunday 10 hours, and we’d still be behind. This year with this process, doing this speed, our volume, of course, keeps growing for e-comm, especially over cyber weekend, and we were able to work about an 8 hour Saturday and get everything completely done. So not only did it save us a lot of labor and headaches and things like that, but from the customer service point of it, of getting those pairs out on a timely basis, has been a home run. And that’s what we were hoping for.”
The initial conveyor accepts manually loaded, filled and sealed assorted size shoe boxes (aka “pairs”), placed narrow or wide edge leading by dimension. The single lane product initially conveys on straight running plastic belt, scaling along the building wall, then overhead inclines on friction top belting, opening up headroom for production floor work space below.
The pairs take a controlled 30’ decline before entering a 180° curve around the wall opening using side flexing chain to stabilize the pairs during the turning process. Pairs then end transfer through another series of sensor-monitored product to maximum accumulation capacity.
Multi-Conveyor’s design engineers built-in an intermediate section of ARB (activated roller belt) to left-justify and gap the pairs with complete accuracy and positioning, precisely timed to feed a new shrink wrapper. The newly wrapped single lane product then discharges at a rate of 40 pairs per minute (PPM) onto an subsequent ARB conveyor with 1:2 divert capability. This system will, again, left-justify and feed two separate lanes of 20 PPM labelers ahead as controlled by the line operators.
As Paul Slotty, Senior Distribution Manager states, “We control lines A or B as needed – diverting to just one running line, for instance, when loading the labeler or a variety other reasons upstream.”
Multi-Conveyor’s electrical engineering team stepped up and took the only onsite upfront technical support reins on calibrating the sensors, timing, controls and communications between OEM equipment.
Jason Russ, Director of Information Systems, elaborates: “I wanted to point out that as we were visualizing how all of this was going to work, we worked very closely with Multi-Conveyor to build the controls so all of these pieces (OEM equipment) can communicate. For example, if one (labeler) line was to go down, we know right away that we need to slow the wrapper down. So the controls that Multi-Conveyor built communicate upstream, tell the wrapper to slow down, tell the ARB table to stop sending pairs (boxes) to this line, so we can figure out what’s going on with the line to get it resolved. When they turn the line back on, the controls tell the wrapper to speed up and tell the ARB table to start going back and forth (diverting) again.”
Mr. Slotty was also quick to point out the strategic placement of various belting integrated throughout the system. “What you see here, this type of belting we have here, we had this over there (at the labelers) when we were doing our application, but, they were sliding around a little bit. So, we put a little bit more grippy belt on it and it’s worked out great.” Friction top belting was replaced in the labeler section, giving the pairs additional grip needed for the label application. That stability created way for an additional discount label application to take place that was previously applied manually.
Post-labelers, Multi-Conveyor added pneumatic actuated reject devices that work in tandem with the customer’s intricate PLC label verification scanning system. Jason explains, “For the reject, when we scan this (pairs), we’re communicating to the PLC that was programmed by Multi-Conveyor to actuate that arm to do the reject of the bad pair.”
By installing a new conveyor system, shrink wrapper and labelers, the company increased output from 6 PPM to 40 PPM, a 556% increase in output. However, the conveyors were spec’d up to 45 PPM, building in a total 650% eligible increase in future growth.
George sums up the experience, “We had never used plastic conveyor before so it was intriguing and nerve racking, but we’re really happy how things turned out. It rides so nice. We’ve had zero downtime with regard to the conveyors, motors and everything. Just from a serviceability standpoint it’s been fantastic. It’s been a really good partnership (with Multi-Conveyor) that we want to continue over the next, many years.”
See this line in action! Then, see even more elaborate conveyor systems by visiting our video gallery. Then, call us at 1-800-236-7960. Or click here to start your next conveyor project. Remember, Multi-Conveyor … your best, conveyed better.
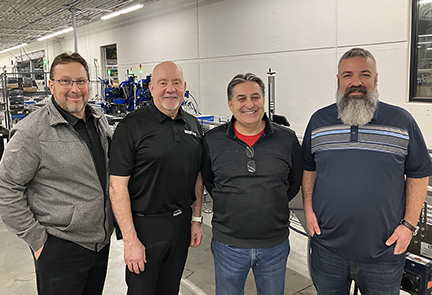
From left: John Arena, Paul Slotty, George Sotiros, Jason Russ
Multi-Conveyor would like to the following Management Staff at Weyco Group for their time, talent and hospitality in the making of this video production:
George Sotiros, Chief Information Officer, VP of Information Systems, VP of Distribution
Paul Slotty, Senior Distribution Manager
Jason Russ, Director of Information Systems
John Arena, Senior Distribution Manager
Kevin Kauphusman, Senior Distribution Manager
For more information on Weyco Group, please visit: www.weycogroup.com
©Multi-Conveyor